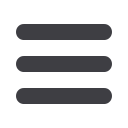
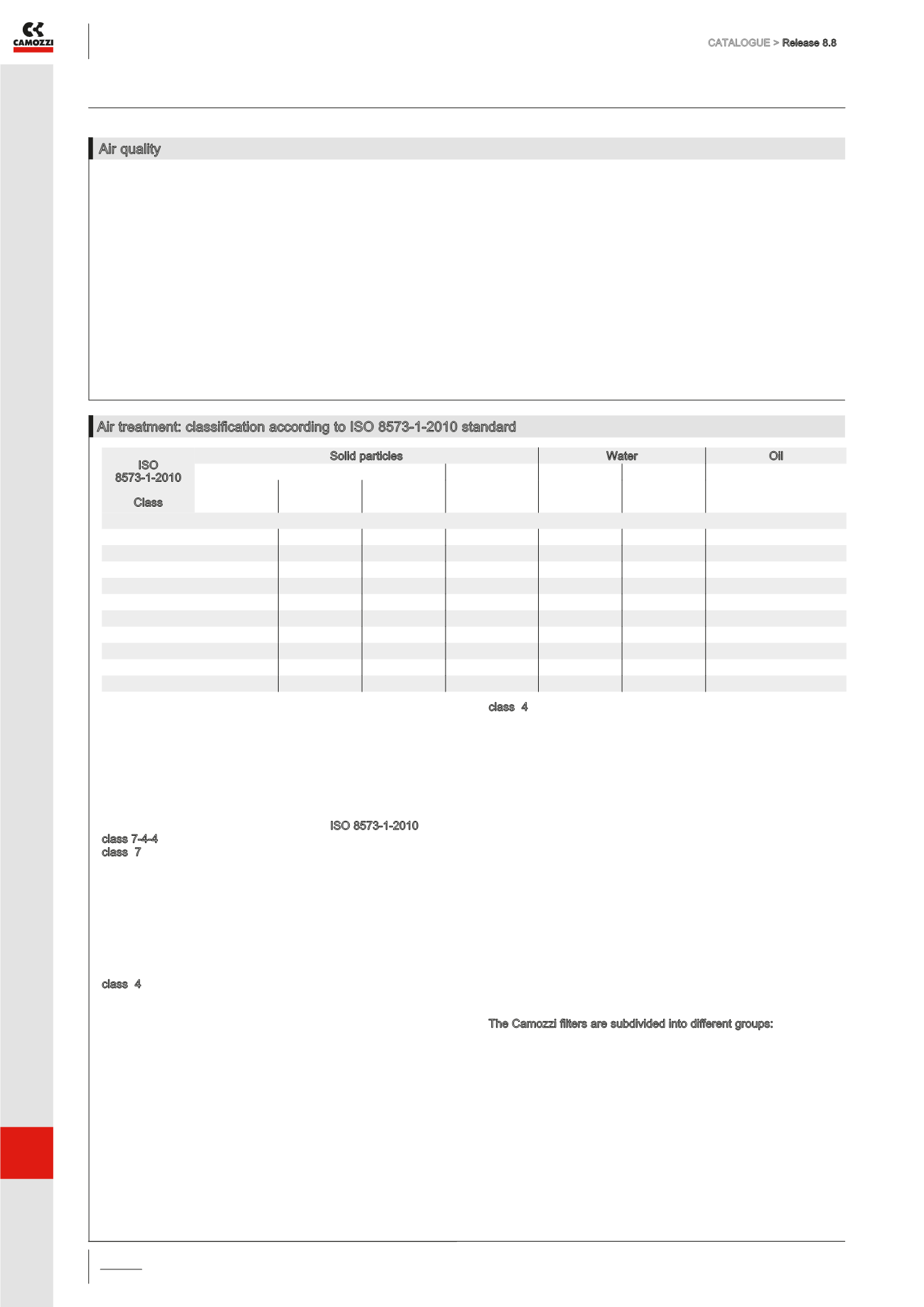
CATALOGUE >
Release 8.8
APPENDIX >
Camozzi products
a
APPENDIX
a
/2.01
Information for the use of Camozzi products
In order to guarantee a proper functioning of its products, Camozzi S.p.A. herewith provides some general information.
Air quality
Beyond respecting the limit values as pressure, force, speed, voltage,
temperature and others values that are indicated in the general tables
of each product, another aspect to consider is the quality of the
compressed air. While resources as electricity, water and gas are
normally supplied by external companies that guarantee the standard,
air is produced inside a company and therefore it’s the user that has
to guarantee its quality.
This characteristic is essential for a proper functioning of pneumatic
systems. One m³ of air at the atmospheric pressure contains various
substances:
- more than 150 million of solid particles with dimensions
from 0,01 µm to 100 µm,
- fumes due to combustion,
- water vapour, which quantity depends from the temperature,
at 30° there are about 30 g/m³ of water
- oil, up to about 0,03 mg
- micro organisms
- as well as different chemical contaminants, odours etc …
Compressing the air, in the same volume of 1 m³, we find “n” m³
of air, therefore the substances indicated before increase.
In order to limit this, at the inlet and outlet of the compressors filters,
driers and oil separators are installed.
In spite of these precautions, the air, during its transport inside tubes
or storage in tanks, can collect flakes of rust, a part of the water
vapour contained in the air, cooling down, can pass from a gaseous
state into a liquid state, but can also transform the oil fumes
that were not retained by the previous filters.
For this reason it is advisable to equip the systems or machinery
with air treatment groups.
Air treatment: classification according to ISO 8573-1-2010 standard
These groups can have different functions: isolation valves,
pressure regulators, soft-start valves and of course filters.
Only in some applications, lubricators are still used.
Regarding filtering, there are standards of reference
as ISO 8573-1-2010 that classify air according to its quality.
This standard defines the relevant class of compressed air according
to the presence of three contaminating categories: solid parts,
water or water vapour, concentration of micro mist or oil vapours.
In general, if not specified otherwise in the characteristics of the single
component, the Camozzi products require an ISO 8573-1-2010
class 7-4-4 air quality, this wording indicates that:
class 7
A maximum concentration of solid particles of 5 mg/m³ is allowed
and the dimension is not declared.
The standard Camozzi filters are declared as class 7 even if the
filtering elements are realized with a technology that enables to
separate solid particles with a dimension of more than 25 µm.
The air exiting from our filters and therefore the air at the inlet of
all other components can contain solid particles with a maximum
concentration of 5 mg/m³ but with a maximum dimension of 25 µm.
class 4
The temperature has to arrive at ≤ 3° in order for the water vapor
to condense and become liquid.
The classical filters have characteristics that separate the humidity
in the air only if it is in a liquid state or nearly.
It is the cooling of the air that enables condensation and then
the elimination of the water present in the form of water vapour.
The air flow entering the bowl of the filter sustains a minimum
expansion phase, (according to the gas law when gas sustains
a sudden expansion its temperature lowers) followed by a vortex,
this enables the heavier particles and the water vapour,
that is condensed due to the expansion, to adhere to the sides
of the bowl and slide down towards the drainage system.
Except for specific versions, the Camozzi filters are declared
to be in class 8.
This means that the user has to provide in installing driers in its
compressed air production system that, by cooling the air, dehumidify it.
class 4
The concentration of oily parts must be of maximum 5 mg/m³.
The compressors use oil that during the process can be introduced
into the system in the form of aerosol, vapour or liquid.
This oil, as all other pollutants, is transported by the air into the
pneumatic circuit, enters in contact with the seals of the components
and subsequently in the environment through the outlets of the
solenoid valves. In this case coalescing filters are used that have an
operating principle and filtering cartridges that are different compared
to others and this allows to aggregate those micro-molecules of oil
suspended in the air and remove them.
The Camozzi coalescing filters enable to reach classes 2 and 1.
It is important to keep in mind that the best performance is reached
only by means of a filtering process with subsequent phases.
As illustrated, there are filters with different characteristics,
a very efficient filter for a certain contaminant, but may not be so
for other contaminants.
The filtering elements determine the class of the filters,
these elements should be replaced after a certain period or after
a certain number of working hours.
These parameters vary according to the characteristics
of the incoming air.
The Camozzi filters are subdivided into different groups:
- Filtering element of 25 µm, class 7-8-4
- Filtering element of 5 µm, class 6-8-4
- Filtering element of 1 µm, class 2-8-2
with pre-filter class 6-8-4
- Filtering element of 0,01 µm, class 1-8-1
with pre-filter class 6-8-4 residual oil content of 0,01 mg/m³
- Activated carbon, class 1-7-1
with pre-filter class 1-8-1 residual oil content of 0,003 mg/m³
The components are previously greased with special products and do
not need an additional lubrication. In case it should be necessary,
use ISO VG 32 oil.
The quantity of oil introduced into the circuit depends on the different
applications, we suggest a dosage of max. 3 drops per minute.
ISO
8573-1-2010
Class
Solid particles
Water
Oil
Max. Number of Particles per m³
Max
Concentration
mg/m³
Water pressure
dew point
°C
Liquid
g/m³
Total content
(liquid, aerosol and vapour)
mg/m³
0,1 - 0,5
µm
0,5 - 1
µm
1 - 5
µm
0
More strict than class 1, defined by the device user
1
≤ 20,000
≤ 400
≤ 10
-
≤ - 70°
-
≤ 0,01
2
≤ 400,000
≤ 6,000
≤ 100
-
≤ - 40°
-
≤ 0,1
3
-
≤ 90,000
≤ 1,000
-
≤ - 20°
-
≤ 1
4
-
-
≤ 10,000
-
≤ + 3°
-
≤ 5
5
-
-
≤ 100,000
-
≤ + 7°
-
-
6
-
-
-
≤ 5
≤ + 10°
-
-
7
-
-
-
5 - 10
-
≤ 0,5
-
8
-
-
-
-
-
0,5 - 5
-
9
-
-
-
-
-
5 - 10
-
X
-
-
-
> 10
-
> 10
-