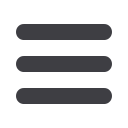
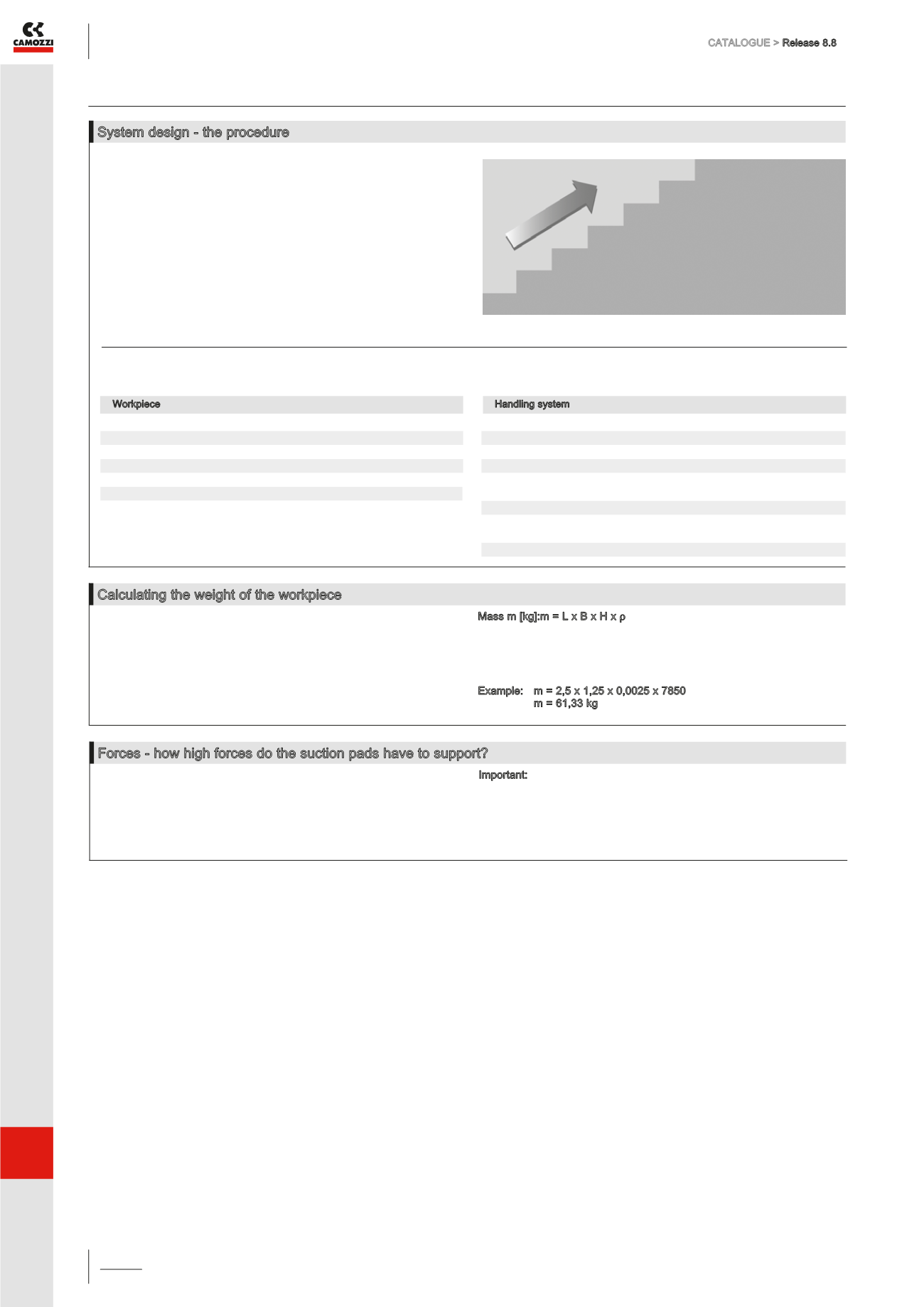
CATALOGUE >
Release 8.8
APPENDIX >
Technical information about products
The calculations in the example are based on the following data:
In this section the design procedure is described for a complete
system step by step.
This exercise is based on a typical design example.
7. Vacuum switch
6. Solenoid valves
5. Vacuum generator
4. Vacuum hose
3. Mounting elements
2. Suction pads
1. Calculation of the forces
Flowchart for system design
Workpiece
Material:
steel sheets, stacked on a pallet
Surface:
smooth, flat, dry
Dimensions: length:
max.2500 mm
width:
max.1250 mm
thickness: max.2,5 mm
weight:
circa 60 kg
Handling system
System used:
portal transfer unit
Available compressed air supply::
8 bar
Control voltage:
24 V DC
Transfer procedure:
horizontal - horizontal
Max. acceleration values
X and Y axes:
5 m/s
2
Z axis:
5 m/s
2
Cycle time:
30 s
Planned times:
for picking up:
<1s
for releasing:
<1s
Calculating the weight of the workpiece
For all subsequent calculations, it is important to know
the mass of the workpiece to be handled.
This can be calculated with the following formula:
Mass m [kg]:m = L x B x H x
ρ
L = lenght [m]
B = width [m]
H = hight [m]
ρ
= density [kg/m
3
]
Example: m = 2,5 x 1,25 x 0,0025 x 7850
m = 61,33 kg
System design - the procedure
Forces - how high forces do the suction pads have to support?
In order to determine the necessary holding forces, the above mass
calculation is needed. In addition, the suction pads must be capable of
handling the acceleration forces which, in a fully automatic system, are
by no means negligible. In order to simplify the calculation, the three
most important and most frequent load cases are shown graphically and
described below.
Important:
In the following simplified representations of the load cases I, II and III,
the worst case with the highest theoretical holding force must always
be used for the subsequent calculations.
a
APPENDIX
a
/3.06
Example of Vacuum calculation